Model Murder!!!
Refering to a previous post, I needed to cut up some metal models and mold them so I can cast them in resin so I can cut away at them more effectively to get the pieces I am wanting for my models.
1) Setting up my model vice and lining up the models to be cut.
2) Using clippers and a small hack saw, I cut them up.

3) The end result.

Converting Cut Models to Resin Copies
This took up most of my time and I still don't know how it will turn out. I will be able to crack the mold toorrow and cast the first resin pieces after work.
1) Creating a mold box from Legos. Golden Lego FTW! lol

2) Since this will need to be a 2 Part Mold, I have to set the models half deep in non-hardening clay.

3) Key holes so the recasting molds will line up again and again.

4) Dry measuring. Casting can be very expensive, so you don't want to waste any material you use. I found this tip to measure volume with dry rice. 2.5oz of rice to 2.5oz of RTV Silicone Base.


5) Weighing 10:1 ratios of RTV Silicone Base and RTV Catalyst.

6) Chemicals ready for mixing and pouring. The cup on the right has been preped with a hole in the cup for the all important "Bombs Away" method. I'll explain later

7) Ready for the garage and yes that is Pam. I'll explain that later too.

8) Setting up the "Bombs Away" method. The "BA" method is a cheap way to avoid acquiring a vacume chamber to suck the air out of the mix. When mixing the chemicals, it is like trying to mix white glue with water. The base silicone is extremely thick and the catalyst is as thin as water. Mixing causes air to get trapped in the silicone. This will cause air bubbles to appear in your mold and on your cast pieces. So you want to get all the air out. Without a couple hundred dollars set aside for a vacume chamber, the only reasonable solution is the "BA" method. Take a paper cup and cut a hole in it about 1/2" diameter near the bottom of the cup. Take a piece of tape and cover the hole. Mix the chemicals together using the 2 cup mixing process and pour the contents into the cup with the hole. Place the cup now holding the chemicals over the edge of a table about 30"-36" high and set your mold box on the floor directly underneath the hole. Pull off the tape and let the contents fall into the mold box below. The silicone comes out in a 1/2" stream but as it falls, the 1/2" stream streaches into about a 1/32"-1/64" stream pushing all the air out. What lands in the mold is practically air free.

Here I used a string with a small weight to place the mold box in the proper location for the pour.

9) "BOMBS AWAY!!!"


10) The result of the first pour. Now I get to let that sit for 24hrs before I can flip it over and remove the clay and pour the other side.

11) THE GOLDEN LEGO HAS FAILED ME!!! The non hardening clay did exactly what it said it would do, not harden. I think the heat from the chemical reaction of the silicone and catalyst caused it to soften more than it should have. I will have to look at alternatives to this brand of clay. Although it came with the kit, you can see the ammount of work that needs to be done to get this shit off.

12) After about 1.5 hours of scrubing with a tooth brush and water, I think I was able to salvage the mold. My concern was that I had to break the mold box pre-maturely and make another. On the plus side, making another one out of Leogs isn't hard and will be the exact same size. The Pam plays a role in this portion of the mold. I need a mold release agent so the fresh silicone does not mold to the exising bottom half of already cured silicone. Pam is a cheaper alternate than official mold release chemicals.

13) Repeate "BA" methond on the other side.

14) The result...won't know until Moday. I have to leave this sit for another 24hrs and since I finished cleaning the mold around 2am Sunday, I won't be able to crack it and cast anything till I get home frome work tomorrow. So stay tuned! I will post more pics tomorrow with the results.
---------------------------------------------
OTHER THINGS I WORKED ON
1) Grey Knight Hero. My GK Hero will be standing upright for his dramatic pose and thus I had to cut up a terminators legs and pin them in what would be a standing straight pose.

After dicing him up, I had to go back in and strengthen his joints with "green stuff" to make sure he doesn't fall apart when I sculpt a robe on him. Don't judge the sculpting job here ok guys? All of this will be covered when I get his robe on.

Here he is next to a typical Grey Knight Terminator. He's going to be a BIG fella! lol

2) Other pieces in the works. One problem I ma having is trying to decide how best to divide my time. I have chemicals curing, "green stuff" drying and glue drying on 5 different things at once. I am constantly hopping back and forth from one item to another. Here in this picture you can see my start on scratch building a correct size shoulder pad with the open book on it and the dagger that will lay on the open book. The two small skulls are for the Arcanite Reaper axe that I am redoing. The first attempt was too big. And you can also see the first layer to the masked cowl that most of the army will have.

3) My wife just checked the mail and my DVDs came! I will be watching these here in just a little bit. Super stoked about these =)

4) I did play a bit of WOW too. I got my troll shaman a level, my alli hunter a level (yay lvl 40!) and played in a few BG's with my lock. I actually played in a WSG match and didn't die a single time!
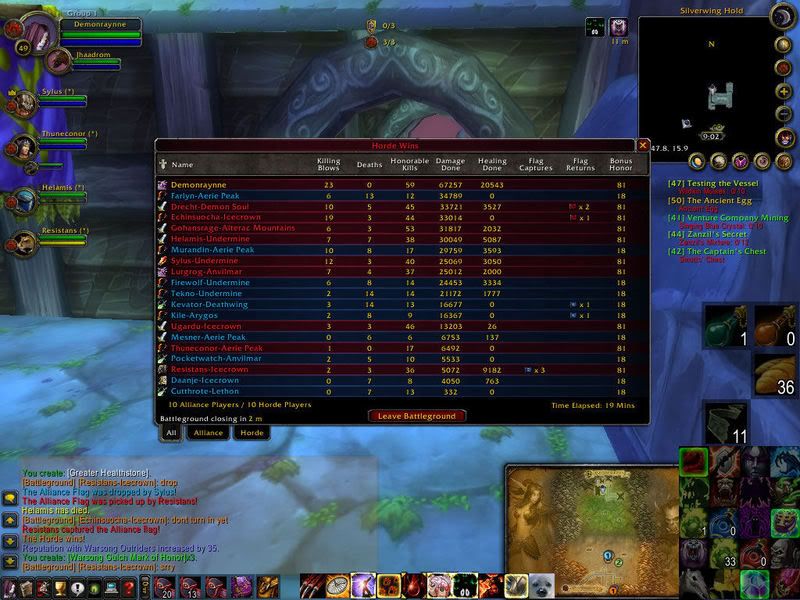
2 comments:
My god, does the geek ever end????? LOLS! Great job, and I like the format. Way more intense than I want to be involved in!
Good lord man! I guess I know what you did your entire weekend. Very impressive, very scary.
Post a Comment